Warehouse location strategy: optimizing your distribution network
.png)
Discover how strategic warehouse location decisions can reduce total logistics costs while improving delivery times. Expert guidance on network optimization.
Key Takeaways
- Strategic warehouse location decisions can reduce total logistics costs by 10-30% while improving delivery times by 15-40%
- Comprehensive network analysis should balance transportation costs (typically 50-70% of logistics spend) against fixed facility expenses
- Optimal network design varies by industry, with most companies now requiring 5-8 strategically placed facilities for national coverage
- Modern location strategy increasingly emphasizes labor availability and quality alongside traditional factors like transportation access
- Strategic partnerships with established warehousing providers can reduce implementation risk while accelerating network optimization
Introduction
Few supply chain decisions have more far-reaching impact than warehouse location strategy. The positioning of your distribution facilities fundamentally shapes transportation costs, inventory requirements, service capabilities, and labor expenses. A thoughtfully designed network creates competitive advantage through both cost efficiency and service excellence, while a suboptimal approach can create a permanent disadvantage that no amount of operational excellence can overcome.
Distribution network design has grown increasingly complex as service expectations rise, transportation costs fluctuate, and labor markets tighten. The days of simple "one central warehouse" solutions have largely disappeared, replaced by sophisticated multi-node networks optimized for specific product and customer requirements. Yet many companies continue to operate legacy networks designed for previous market conditions, missing opportunities for significant improvement.
This guide explores modern approaches to warehouse location strategy, examining key decision factors, analytical methodologies, and implementation approaches. Whether you're designing a new distribution network or optimizing an existing one, these principles and practices will help you develop a warehouse location strategy that creates sustainable competitive advantage in today's demanding business environment.
Fundamental principles of location strategy
Effective warehouse location strategy begins with understanding the fundamental principles that drive network performance. These principles provide the foundation for more detailed analysis and decision-making.
The transportation cost imperative
Transportation typically represents 50-70% of total logistics costs for most businesses, making it the dominant factor in network design. Effective warehouse location strategy starts with minimizing overall transportation expense by positioning facilities to optimize both inbound and outbound movement:
- Customer proximity: Locating warehouses to minimize distance to major customer concentrations
- Supply chain alignment: Positioning relative to manufacturing plants and key suppliers
- Modal optimization: Placing facilities to leverage advantageous transportation options
- Lane balance: Minimizing empty miles and maximizing equipment utilization
- Service alignment: Ensuring transportation capabilities match service requirements
Because transportation costs generally increase linearly with distance while fixed facility costs benefit from economies of scale, most network designs prioritize fewer, larger facilities than might seem intuitive from a pure transportation perspective. The optimal design balances these competing factors to minimize total cost.
Inventory-location relationships
Warehouse location decisions directly impact inventory requirements through several mechanisms:
- Risk pooling: Fewer facilities generally reduce total inventory through statistical aggregation
- Lead time effects: Facilities closer to customers enable lower safety stock while maintaining service levels
- Replenishment efficiency: Strategic positioning can reduce replenishment lead times and variability
- Specialization opportunities: Multiple facilities enable inventory specialization based on demand patterns
The inventory implications of network design can represent 10-30% of total inventory investment, a significant consideration for working capital and storage requirements. Advanced network analysis explicitly models these inventory effects rather than focusing solely on transportation and facility costs.
The labor equation
Labor availability and cost have become increasingly critical factors in warehouse location decisions:
- Workforce availability: Sufficient qualified workers within reasonable commuting distance
- Wage rates: Competitive compensation levels for distribution operations
- Labor quality: Productivity, turnover, and workforce stability considerations
- Competition: Presence of other warehousing operations competing for talent
- Workforce development: Available training resources and educational infrastructure
In today's challenging labor environment, these considerations often override marginal transportation advantages in final location decisions. Companies increasingly select locations with slight transportation cost penalties but significant labor advantages, recognizing that workforce issues can create operational constraints that no amount of theoretical efficiency can overcome.
Network modeling and optimization approaches
Beyond fundamental principles, effective warehouse location strategy employs sophisticated modeling techniques to identify optimal network configurations.
Data requirements for effective modeling
Comprehensive network analysis requires accurate data across multiple dimensions:
- Customer locations and volumes: Detailed ship-to points with annual quantities
- Supplier locations and volumes: Origin points for inbound materials
- Transportation rates: Accurate costs for all relevant lanes and modes
- Service requirements: Specific delivery time expectations by customer segment
- Facility costs: Realistic expenses for potential locations, including labor, real estate, and utilities
- Handling costs: Location-specific expenses for product movement and processing
- Inventory carrying costs: Financial parameters for working capital computation
The quality of network modeling results directly reflects the quality of input data. Companies with the most successful network designs invest significant effort in data collection and validation before beginning the analytical process.
Greenfield analysis
For companies starting with minimal constraints, greenfield analysis determines theoretically optimal facility locations based purely on distribution economics:
- Demand mapping: Visualizing customer locations and volumes
- Center of gravity analysis: Identifying mathematical optimums for minimizing weighted distances
- Constraint application: Adding practical limitations like facility availability and transportation infrastructure
- Cost modeling: Calculating total landed cost for various scenarios
- Sensitivity testing: Evaluating how changes in key variables affect optimal locations
This analysis typically begins with a clean-slate approach, then incorporates real-world constraints to develop practical recommendations. While few companies implement pure greenfield recommendations without modification, this analysis provides a valuable baseline for understanding potential opportunities.
Network rationalization
For companies with existing facilities, network rationalization evaluates improvement opportunities within current constraints:
- Current state assessment: Analyzing performance of the existing network
- Gap identification: Determining specific improvement opportunities
- Scenario development: Creating practical options for network enhancement
- Financial modeling: Quantifying costs and benefits of various approaches
- Transition planning: Defining implementation approaches for recommended changes
This pragmatic approach often identifies significant improvements without requiring complete network redesign. For many organizations, network rationalization delivers 50-70% of theoretical greenfield benefits with substantially lower implementation costs and disruption.
Simulation and scenario planning
Modern network analysis extends beyond static modeling to incorporate simulation and scenario planning:
- Demand variability analysis: Testing network performance under different volume scenarios
- Service failure simulation: Identifying vulnerable points and contingency requirements
- Cost sensitivity modeling: Understanding the impact of transportation or labor cost changes
- Growth scenario planning: Evaluating network performance under various growth projections
- Disruption response modeling: Testing resilience against supply chain disruptions
These advanced techniques help create networks that perform well not just under current conditions but across a range of potential future scenarios. The most robust designs maintain acceptable performance even when key assumptions change significantly.
Geographic strategies for warehouse placement
Different geographic approaches to warehouse location create distinct service capabilities and cost structures. Understanding these strategies helps identify the most appropriate approach for your specific requirements.
National distribution center approach
Some companies still utilize a single national distribution center (NDC) strategy:
- Appropriate for: Products with lower value-to-weight ratios, limited service time sensitivity, or highly unpredictable demand
- Typical locations: Central positions like Cincinnati or Indianapolis that minimize total transportation distance
- Advantages: Maximum inventory aggregation, operational simplicity, lowest facility costs
- Disadvantages: Limited service capabilities, higher transportation costs, vulnerability to disruption
While less common than in previous decades, this approach still works well for certain product categories, particularly those with unpredictable demand across a broad SKU range where inventory aggregation benefits outweigh transportation cost penalties.
Regional distribution strategy
The most common approach today involves regional distribution centers (RDCs) serving defined geographic territories:
- Appropriate for: Products requiring 1-2 day delivery, moderate-to-high volumes, predictable regional demand
- Typical configuration: 5-8 strategically positioned facilities for national coverage
- Advantages: Good service-cost balance, reasonable inventory efficiency, transportation optimization
- Disadvantages: More complex operations, higher facility costs, some inventory disaggregation
This strategy typically positions facilities in major markets or at strategic transportation hubs. Common locations include the Northeast, Southeast, Midwest, South Central, Northwest, and Southwest regions, with exact positioning optimized for specific customer and supplier locations.
Hub-and-spoke networks
More sophisticated distribution networks often employ hub-and-spoke designs:
- Central hubs: Larger facilities handling inventory aggregation and large-quantity distribution
- Regional spokes: Smaller facilities focused on last-mile delivery and service
- Flow patterns: Efficient movement between hubs, with strategic deployment to spokes
- Inventory strategy: Core inventory at hubs with fast-moving items positioned at spokes
This approach combines the inventory efficiency of centralized facilities with the service capabilities of distributed operations. It works particularly well for omnichannel retailers and distributors serving both large business customers and smaller end users with varying service needs.
Multi-echelon networks
The most complex warehouse location strategies involve multi-echelon networks with specialized facility roles:
- Inbound consolidation centers: Facilities near ports or manufacturing concentrations that aggregate supply
- Central distribution facilities: Core warehouses handling storage and distribution to forward locations
- Forward deployment centers: Smaller facilities positioned for rapid customer delivery
- Return processing centers: Specialized locations for reverse logistics operations
These sophisticated networks optimize each facility for its specific role rather than creating identical operations in different locations. While more complex to manage, they often deliver superior service levels with lower total costs for complex supply chains serving diverse customer needs.
Implementation approaches for network optimization
Developing an optimal warehouse location strategy has limited value without effective implementation. Several approaches help translate analytical recommendations into operational reality.
Build vs. lease considerations
One fundamental implementation decision involves facility acquisition approach:
- Build-to-suit development: Custom facilities designed for specific requirements
- Existing building leasing: Occupying already-constructed facilities
- Speculative space: Using recently developed properties awaiting tenants
- Building purchase: Acquiring existing facilities outright
Each approach offers distinct advantages. Build-to-suit provides optimal specifications but requires time for development. Existing buildings offer faster implementation but may require compromise on features. Financial considerations like capital availability and tax implications also influence this decision.
3PL partnership strategies
Many companies implement network optimization through third-party logistics partnerships rather than operating facilities themselves:
- Contract warehousing: Dedicated facilities operated by 3PLs under multi-year agreements
- Public warehousing: Shared facilities with flexible space allocation
- Dedicated operations within multi-client facilities: Committed space within larger 3PL operations
- Integrated transportation-warehousing solutions: Combined services from a single provider
These approaches reduce capital requirements and implementation timelines while leveraging 3PL expertise. They prove particularly valuable when entering new markets or implementing significant network changes where risk management becomes critical.
Phased implementation strategies
Network optimization typically requires phased implementation to manage transition risks:
- Pilot location implementation: Testing the approach at a single facility before broader rollout
- Parallel operations: Maintaining existing facilities while ramping up new locations
- Sequential regional transition: Implementing changes one region at a time
- Product-based phasing: Moving specific product categories in planned sequences
- Customer migration planning: Carefully transitioning customers to new service locations
This measured approach minimizes service disruption while allowing for adjustment based on initial results. The most successful implementations include detailed transition risk management plans with specific contingency approaches for potential issues.
Network evolution planning
Distribution requirements continually evolve with business changes, requiring ongoing network refinement:
- Volume trigger planning: Predefined decision points for network expansion
- Service enhancement roadmaps: Planned evolution to meet increasing expectations
- Flexibility preservation: Maintaining options for adjustment as requirements change
- Regular network assessment: Scheduled review of performance and improvement opportunities
- Continuous improvement processes: Ongoing optimization within the established framework
Rather than viewing warehouse location strategy as a one-time exercise, leading companies establish systematic approaches for network evolution that accommodate growth, changing customer requirements, and market shifts without requiring complete redesign.
Specialized location considerations
Beyond general principles, certain specialized considerations influence warehouse location decisions for specific industries or requirements.
Industry-specific location factors
Different industries have unique location requirements:
- Food and beverage: Temperature-controlled capabilities, food safety compliance, proximity to production
- Retail: Store proximity, rapid replenishment capabilities, seasonal flexibility
- Automotive: Just-in-time delivery to production, sequencing capabilities, supplier proximity
- Industrial products: Heavy load handling, specialized equipment, technical workforce
- Aerospace: Security requirements, quality control capabilities, specialized handling
Understanding these industry-specific factors ensures warehouse locations support unique business requirements beyond general distribution efficiency.
International distribution considerations
Companies with global operations face additional location considerations:
- Customs and free trade zones: Positioning to minimize duties and taxes
- Port and gateway access: Efficient connections to international transportation
- Cross-border documentation: Capabilities for international shipping compliance
- Country-specific regulations: Alignment with varying national requirements
- Currency and financial implications: Managing international financial exposure
International distribution networks require specialized expertise in global trade regulations and practices. Partnerships with experienced providers often prove valuable for navigating these complex requirements.
E-commerce fulfillment requirements
The growth of e-commerce has created specific location requirements for fulfillment operations:
- Parcel carrier proximity: Close relationships with UPS, FedEx, and other providers
- Last-mile optimization: Positioning for cost-effective residential delivery
- Labor availability: Sufficient workforce for labor-intensive picking operations
- Space for automation: Appropriate facilities for fulfillment technology
- Returns processing capabilities: Infrastructure for managing reverse flows
These specialized requirements often lead to different optimal locations for e-commerce fulfillment compared to traditional wholesale or retail distribution, driving many companies toward multi-channel distribution networks.
Frequently asked questions
How many distribution centers do most companies need for effective national coverage?
Most companies serving the entire United States now utilize 5-8 strategically located distribution centers for optimal coverage, though this varies by industry and service requirements. Companies with next-day delivery requirements typically need 5-7 facilities to reach most major markets, while those with two-day service standards can often achieve coverage with 3-5 well-positioned warehouses. Organizations with same-day delivery requirements might need 15-25 facilities for major market coverage. The optimal number depends on specific service promises, product characteristics, and cost structure.
What are the most important factors in warehouse location decisions?
While transportation optimization remains fundamental, labor availability has become increasingly critical in recent years. The ideal analysis balances multiple factors: inbound and outbound transportation costs (typically 50-70% of total logistics expense), labor availability and cost (particularly critical in today's tight labor market), real estate and facility expenses (including utilities and taxes), proximity to customers and suppliers, and infrastructure quality (including highway access, utilities, and telecommunications). The specific weighting of these factors varies by industry and business model, requiring customized analysis rather than generic recommendations.
How often should companies reevaluate their distribution network?
Most organizations should conduct comprehensive network analyses every 3-5 years, with more frequent reviews triggered by significant business changes. Specific events warranting immediate reevaluation include: business acquisitions or divestitures that substantially change volume or geographic distribution, major customer or channel shifts, significant changes in service requirements, substantial transportation cost increases, facility lease expirations or capacity constraints, and major technology implementations that change operational capabilities. Regular assessment helps identify opportunities for improvement before they become competitive disadvantages.
What are the typical cost savings from network optimization?
Well-executed network optimization typically reduces total logistics costs by 10-30% while improving service levels. Transportation costs usually decrease by 15-25% through more efficient positioning, inventory investment often drops by 10-20% through improved deployment, and labor and facility costs may change based on specific circumstances. Service improvements typically include 15-40% reductions in average delivery time to customers, along with more consistent performance. The financial impact varies significantly based on current network efficiency and specific business requirements, making customized analysis essential.
Should we operate our own facilities or partner with warehouse providers?
The decision between self-operation and third-party partnerships depends on several factors: whether distribution represents a core competency for your organization, available capital for facility investment, desired control level over day-to-day operations, geographic flexibility requirements, and specialized capability needs. Many companies find that contract warehousing partnerships provide an optimal balance—delivering professional operations without capital investment while maintaining substantial control through detailed agreements. The most strategic approach often involves selective outsourcing, with some facilities operated internally and others managed by specialized providers based on specific market and capability requirements.
Recent blogs
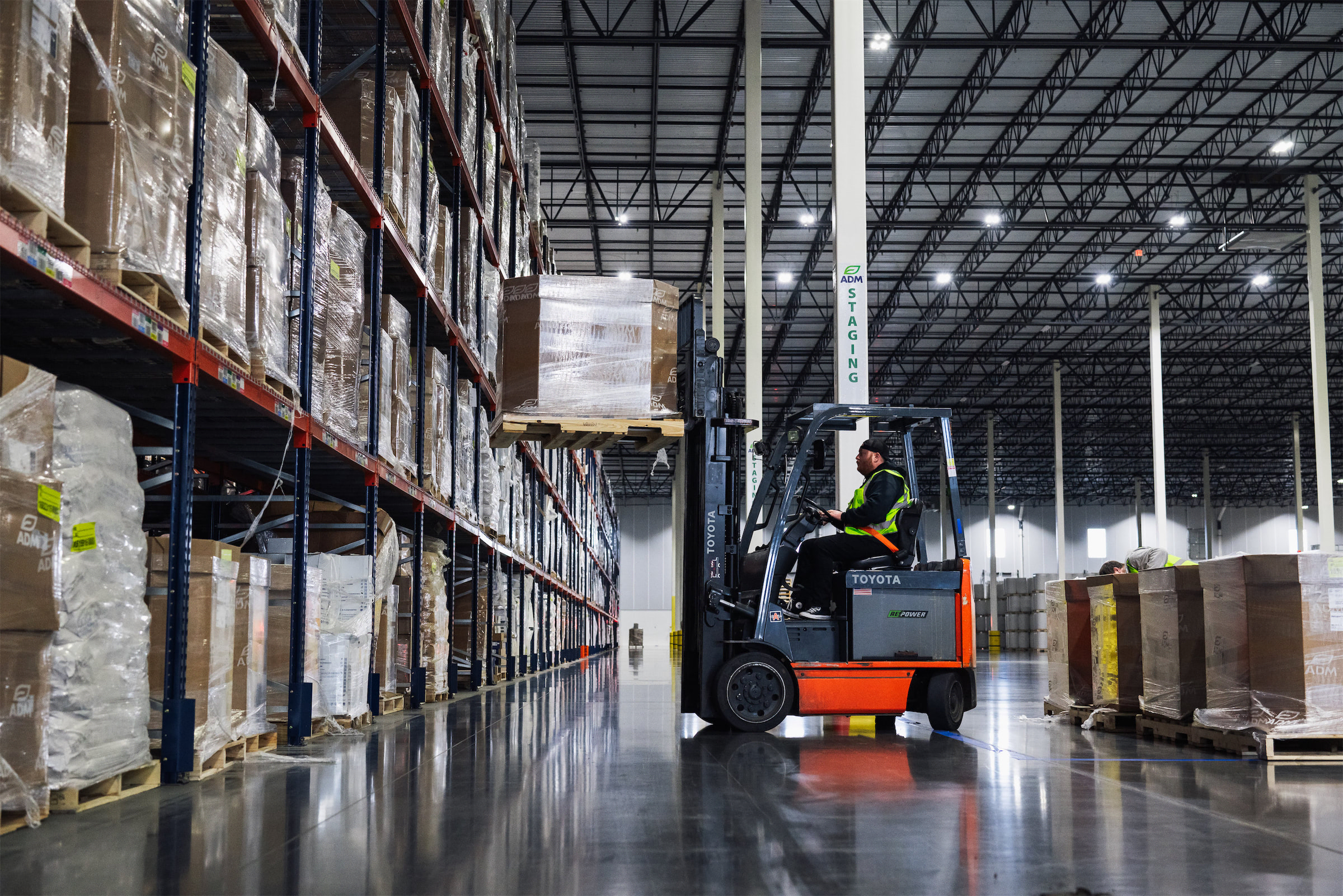
Peak Season Playbook: Scaling Warehouse Operations
Every operations manager knows the peak season paradox: you need double the warehouse capacity and triple the labor force for three months, but you can't afford to maintain those resources year-round. This guide reveals proven strategies for scaling efficiently during demand spikes while controlling costs.
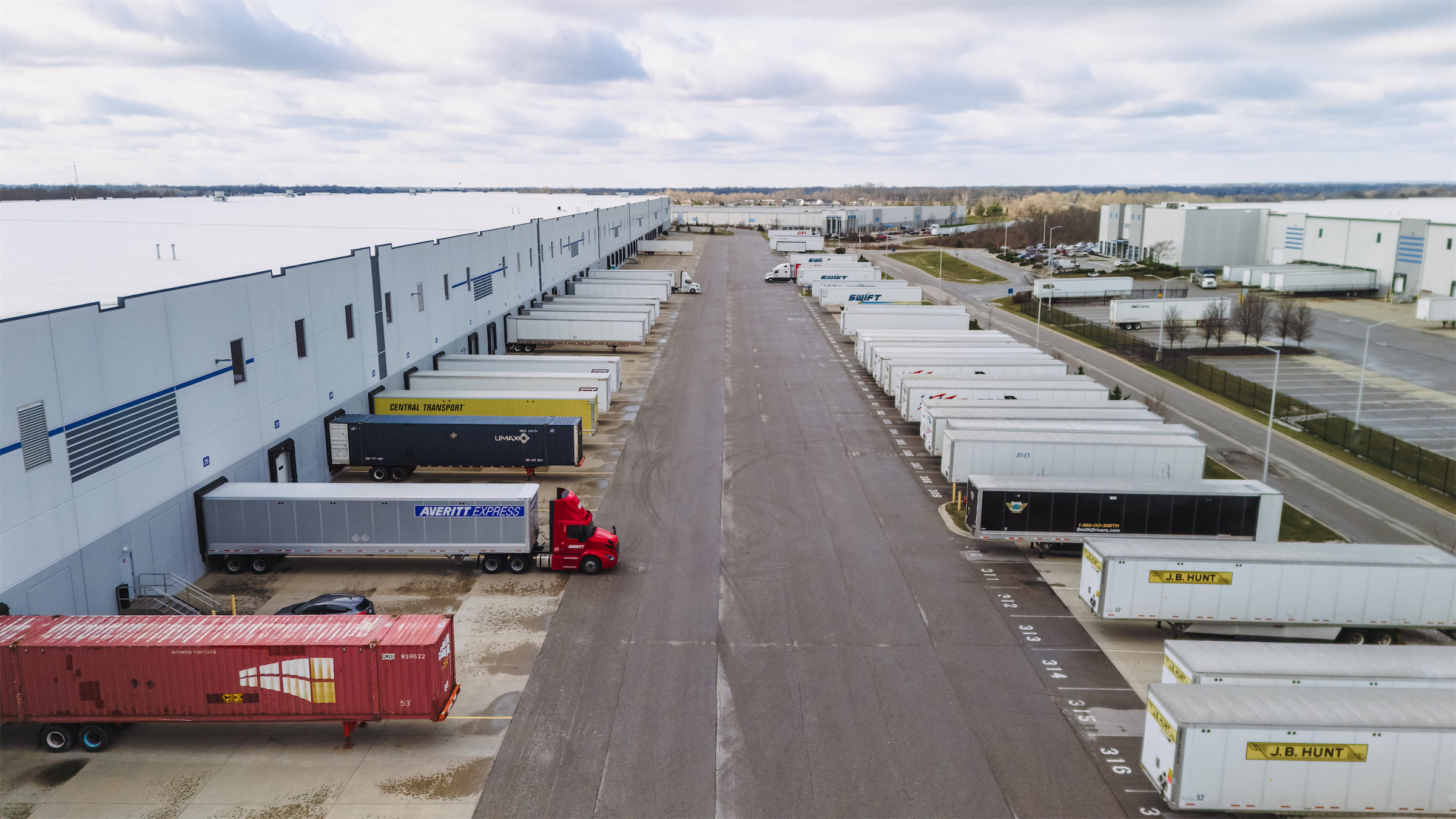
Build vs. Buy: The CFO's Guide to Warehousing Decisions
The warehousing decision facing your company seems straightforward: build your own facility or outsource to a third-party logistics provider. But the financial implications extend far beyond comparing lease rates to construction costs, impacting everything from balance sheet structure to operational flexibility.
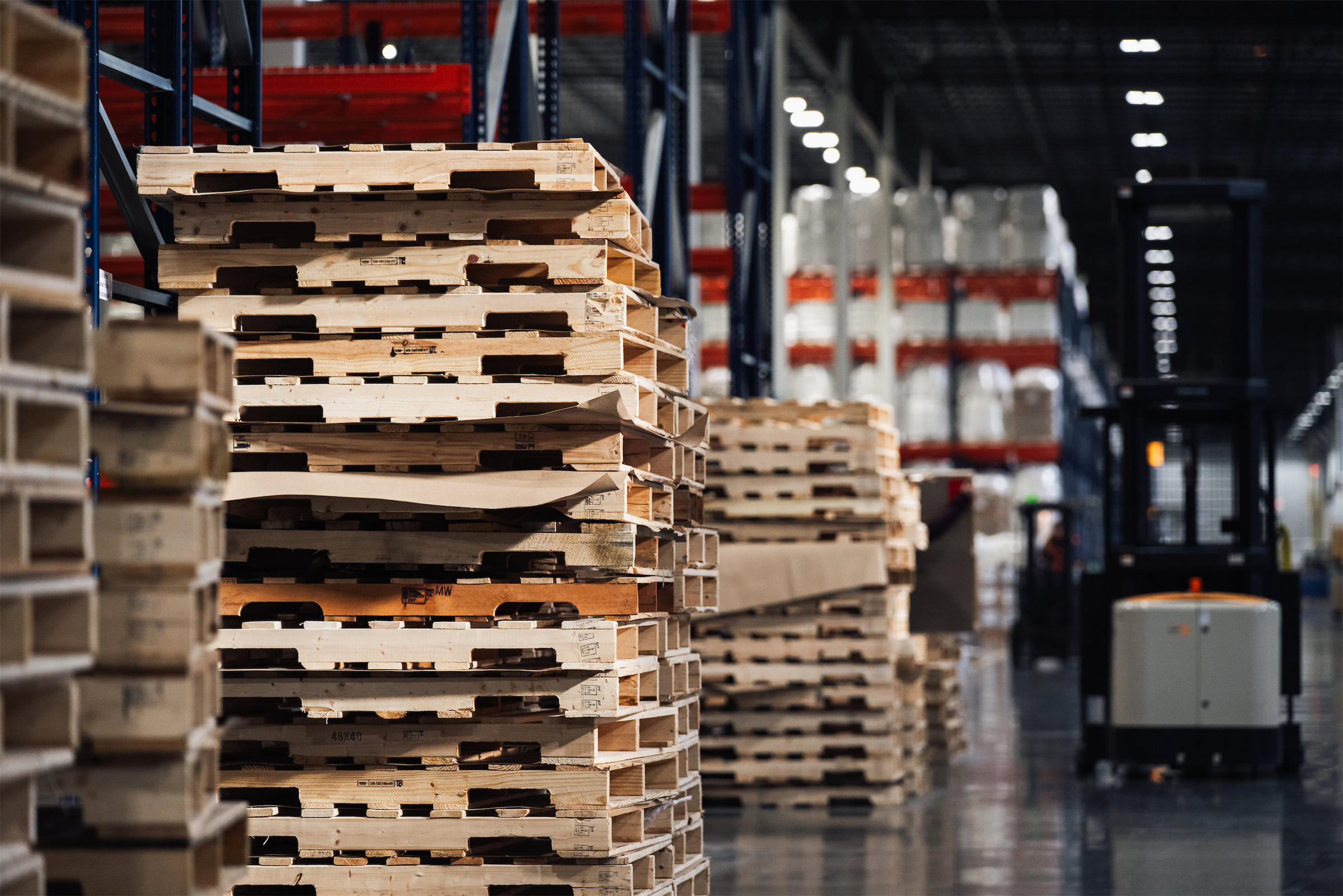
Omnichannel Fulfillment for CPG Brands: Unifying B2B and D2C from One Warehouse
Managing separate B2B and D2C fulfillment operations doubles complexity while fragmenting inventory visibility. Learn how unified omnichannel warehousing eliminates inefficiencies, prevents channel conflicts, and positions CPG brands for sustainable growth.
Arrange a visit
See the Commonwealth difference in action
We believe the best way to understand our capabilities is to experience them firsthand. We invite you to tour one of our facilities, meet our team, and discover how Commonwealth can optimize your logistics operations. Let us show you why so many businesses trust us with their supply chain needs.