Warehouse design solutions: optimizing space & efficiency
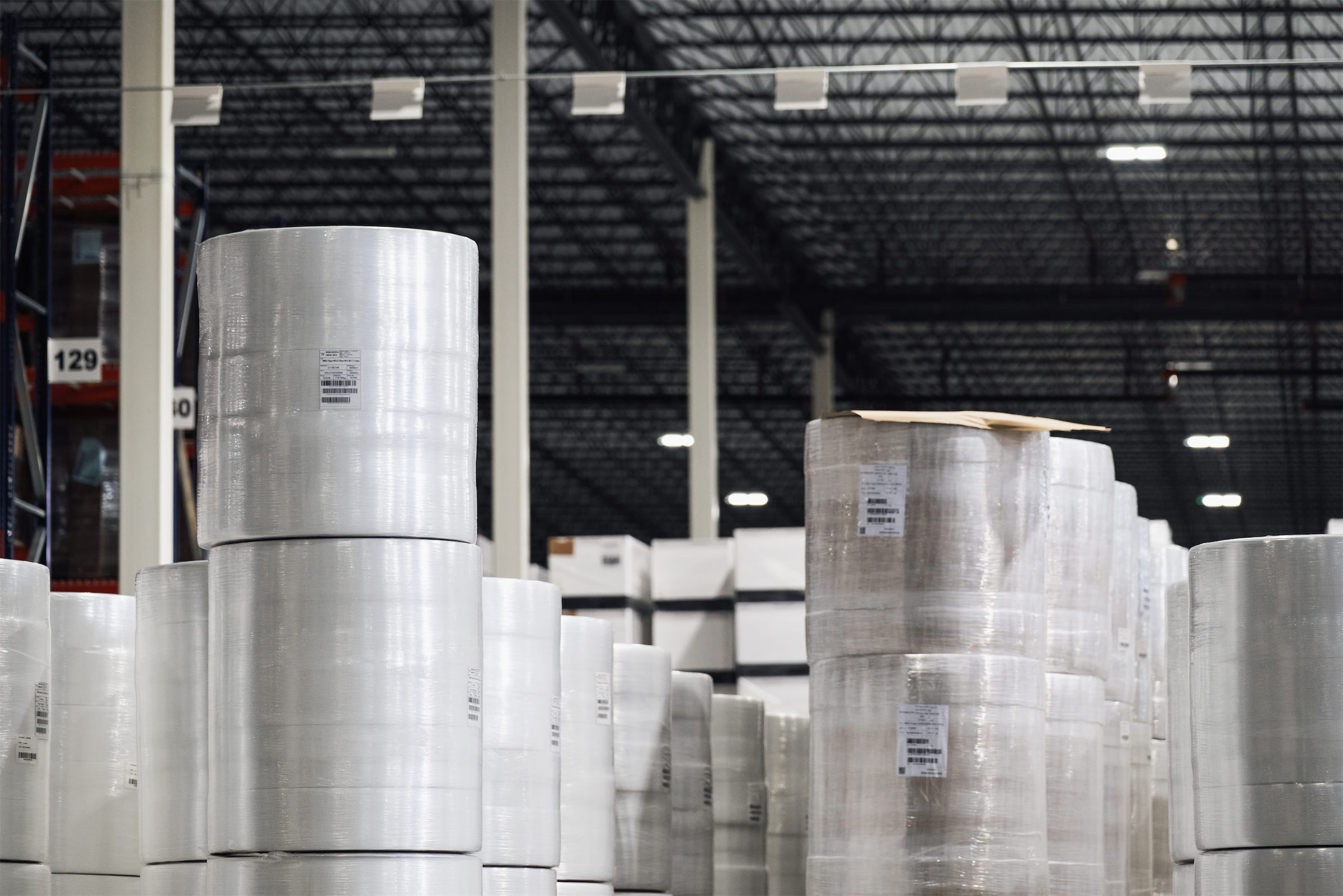
Discover how strategic warehouse design solutions can increase storage capacity while reducing picking times. Expert guidance on layout planning and implementation.
Key Takeaways
- Effective warehouse design can increase storage capacity by 15-30% while reducing picking times by up to 50%
- Strategic layout planning should prioritize product velocity, minimizing travel distances for fast-moving items
- Vertical space utilization through appropriate racking systems can double storage capacity in the same footprint
- Receiving and shipping areas require careful dimensioning based on inventory turnover and peak period analysis
- Modern warehouse designs incorporate flexibility to adapt to changing business needs and technological advancements
Introduction
Warehouse design might not seem glamorous, but it's one of the most critical factors determining operational efficiency and cost-effectiveness in your supply chain. Poor warehouse design creates daily frustrations—congested aisles, wasted space, excessive travel time, and picking inefficiencies that drain resources and limit growth. On the other hand, thoughtful design transforms these same spaces into strategic assets that support business objectives while minimizing operational costs.
Warehouse design solutions encompass far more than simply selecting rack types or determining aisle widths. They represent comprehensive approaches to space utilization, workflow optimization, and operational efficiency that impact every aspect of warehouse performance. From initial concept development through detailed layout planning to implementation and continuous refinement, proper design methodology creates measurable advantages in storage density, labor productivity, accuracy, and flexibility.
Whether you're building a new facility, renovating an existing warehouse, or simply looking to optimize your current operations, understanding the principles and methodologies of effective warehouse design is essential. This guide explores key considerations, proven approaches, and innovative solutions that can transform your warehousing operations from a necessary expense into a genuine competitive advantage.
Core principles of effective warehouse design
Successful warehouse design begins with understanding and applying fundamental principles that have proven effective across diverse operations and industries. While each facility has unique requirements, these core principles provide a foundation for optimization regardless of specific circumstances.
Product velocity-based design
The Pareto principle (80/20 rule) applies strongly in warehouse operations—typically, 20% of your products generate 80% of picking activity. Effective warehouse design acknowledges this reality by:
- Positioning high-velocity items in prime locations with easy access
- Placing frequently paired items near each other to reduce travel
- Creating specialized zones for very fast-moving products
- Relegating slow-moving inventory to more remote storage areas
This velocity-based approach minimizes the average travel distance for most picking activities, significantly improving labor efficiency. Analysis of order history and item movement patterns should directly inform layout decisions, with clear prioritization based on activity levels rather than product categories or other arbitrary groupings.
Maximizing vertical space
One of the most commonly underutilized resources in warehousing is vertical space. Effective designs maximize cube utilization through:
- High-bay racking systems that extend storage vertically
- Multi-level picking systems for smaller items
- Appropriate material handling equipment matched to storage height
- Mezzanines for creating additional processing or storage areas
When evaluating vertical storage options, consider not just the equipment cost but the significant value of the additional square footage gained. A warehouse that effectively utilizes vertical space can often store twice the inventory in the same footprint as a poorly designed facility, dramatically improving space utilization economics.
Future flexibility
Business requirements change, often more rapidly than anticipated. Forward-thinking warehouse design incorporates flexibility to accommodate evolving needs:
- Modular design approaches that allow reconfiguration
- Standardized dimensions that support multiple usage scenarios
- Clear-span construction that minimizes fixed obstacles
- Infrastructure planning for future technology implementation
This flexibility principle applies to both new construction and redesign projects. While purpose-built facilities for current needs might seem efficient initially, they often become constraints when business requirements inevitably change. Building in adaptability, even at some incremental cost, typically delivers significant long-term value.
Strategic layout planning methodology
Beyond fundamental principles, a structured methodology for layout planning ensures comprehensive consideration of all relevant factors. This systematic approach translates principles and requirements into concrete design decisions.
Requirements analysis and data collection
Effective layout planning begins with thorough requirements analysis, including:
- Order profiles: Volume, composition, timing patterns
- Inventory analysis: SKU count, dimensions, storage requirements
- Throughput requirements: Peak and average units per day
- Special handling needs: Temperature control, hazardous materials, security
- Service requirements: Value-added services, customization, kitting
For existing operations, collecting and analyzing historical data provides the foundation for informed design decisions. For new operations, careful forecasting and benchmarking from similar facilities help establish reasonable planning parameters.
The most successful warehouse design solutions incorporate both quantitative data analysis and qualitative input from operational staff. Warehouse associates often provide invaluable insights into workflow challenges and improvement opportunities that might not be apparent from data alone.
Functional area dimensioning
With requirements clearly established, determining appropriate dimensions for each functional area becomes possible. Critical areas requiring specific dimensioning include:
- Receiving area: Sized based on inbound volume, staging requirements, and processing time
- Storage zones: Dimensioned by inventory volume, SKU count, and storage media
- Picking areas: Sized according to order volume, picking methodology, and staffing
- Value-added processing areas: Dimensioned based on service requirements and workflow
- Shipping area: Sized according to outbound volume, staging needs, and carrier requirements
Each area's dimensions should reflect both average requirements and peak capacity needs, with appropriate buffers for variability. For operations with significant seasonality, such as those serving consumer packaged goods or retail customers, planning for peak periods is essential, potentially with flexible spaces that serve different functions during on and off-peak seasons.
Storage media selection
Selecting appropriate storage systems dramatically impacts both space utilization and operational efficiency. Common options include:
- Selective racking: Offers 100% SKU accessibility but lower density
- Double-deep racking: Increases density with some accessibility trade-offs
- Drive-in/drive-through racking: High density for limited SKU applications
- Push-back racking: Good balance of density and selectivity
- Pallet flow racking: Excellent for FIFO operations with high volume
- Mobile racking: Maximum density with full accessibility, at higher cost
- Automated storage and retrieval systems: Highest density and throughput
The optimal solution often involves multiple storage types within the same facility, each matched to specific inventory characteristics and operational requirements. For example, high-velocity items might utilize selective racking for maximum accessibility, while slow-moving items could be stored in higher-density systems to maximize space utilization.
Activity relationship planning
Beyond individual area dimensioning, the relationships between different warehouse activities significantly impact overall efficiency. Activity relationship planning evaluates the flow between functional areas and positions them to minimize unnecessary movement and maximize synergies.
This planning typically uses relationship charts that quantify the importance of proximity between different activities. For instance, receiving and quality control might have a "critical" proximity relationship, while receiving and shipping might have only an "important" relationship in a U-shaped flow or an "unimportant" relationship in a linear flow design.
For contract warehousing operations handling diverse client requirements, these relationships become particularly complex and require careful analysis to optimize. The best designs balance the theoretical ideal with practical constraints such as column spacing, dock door locations, and utility access.
Implementation considerations for warehouse designs
Even the best-conceived warehouse design delivers value only through effective implementation. Several critical factors influence implementation success and should be incorporated into the planning process.
Phased implementation approaches
For redesigns of existing operations, phased implementation often provides the best balance between improvement and operational continuity. Effective phasing strategies include:
- Segmenting the facility into zones for sequential redesign
- Implementing changes during seasonal low periods
- Temporary relocation of inventory during renovation
- After-hours or weekend implementation for critical changes
The phasing strategy should prioritize improvements with the highest ROI while minimizing disruption to ongoing operations. This balanced approach often delivers better overall results than attempting a complete redesign in a single implementation phase.
Material handling equipment integration
Storage systems and material handling equipment must work together as an integrated system. Implementation planning should address:
- Equipment specifications matched to storage heights and configurations
- Aisle widths appropriate for selected equipment
- Charging infrastructure for electric equipment
- Maintenance access considerations
- Operator training requirements
The industrial products handled in your facility also influence equipment selection. Heavy or oversized items require specialized handling equipment that must be accommodated in the warehouse design.
Technology infrastructure planning
Modern warehouse operations rely heavily on technology systems that require appropriate infrastructure. Implementation planning should include:
- Network connectivity throughout the facility
- RF coverage for wireless devices
- Power access for charging stations and equipment
- Mounting points for scanners, displays, and other technology
- Server room or data closet requirements
For warehouses incorporating automation or robotics, these infrastructure requirements become even more critical and complex. Failing to plan adequately for technology infrastructure often creates significant limitations and retrofit costs later.
Change management and training
The human element represents a crucial factor in successful warehouse design implementation. Comprehensive change management should include:
- Early stakeholder involvement in the design process
- Clear communication of changes and rationale
- Thorough training on new processes and equipment
- Performance support during the transition period
- Feedback mechanisms for continuous improvement
Operational staff who will work within the new design should have input during the planning process. Their involvement not only improves the design by incorporating frontline insights but also increases buy-in and adoption during implementation.
Future-proofing your warehouse design
Warehousing continues to evolve rapidly, with new technologies and methodologies emerging regularly. Future-proofing your design ensures it remains effective as business requirements and capabilities change.
Automation readiness
Even if full automation isn't part of your immediate plans, designing for automation readiness preserves future options. Key considerations include:
- Floor flatness and levelness to support automated equipment
- Column spacing that accommodates automated systems
- Clear height for potential automated storage systems
- Power capacity for automation equipment
- Network infrastructure for control systems
These design elements generally add minimal cost during initial construction but preserve valuable options for future enhancement. For operations in locations with labor challenges, such as Cincinnati or West Chester, this automation readiness can be particularly valuable as labor markets evolve.
Sustainability and energy efficiency
Future-oriented warehouse designs increasingly incorporate sustainability elements that deliver both environmental and economic benefits:
- Energy-efficient lighting with intelligent controls
- HVAC systems matched to actual usage patterns
- Insulation appropriate for local climate conditions
- Renewable energy infrastructure where appropriate
- Water conservation systems for applicable facilities
Many of these sustainability elements deliver positive ROI while also supporting corporate environmental goals and reducing long-term operating costs. They should be considered integral elements of forward-thinking warehouse design rather than optional add-ons.
Scalability considerations
Business growth often outpaces forecasts, making scalability a critical design consideration. Effective approaches to scalability include:
- Modular design that allows for building expansion
- Phased implementation planning for future growth
- Infrastructure sized for potential expansion
- Clear-span construction that maximizes future flexibility
- Site planning that preserves expansion options
Even if immediate growth isn't anticipated, preserving these options through thoughtful initial design typically requires minimal investment while creating significant future value.
Frequently asked questions
How much can effective warehouse design improve operational efficiency?
Well-executed warehouse design typically yields 15-30% improvements in labor efficiency through reduced travel time, optimized workflows, and improved ergonomics. Storage capacity often increases by 10-40% through better space utilization and appropriate storage media selection. These improvements translate directly to lower operating costs and increased capacity within the same footprint.
What is the ROI timeframe for a major warehouse redesign project?
Most comprehensive warehouse redesign projects deliver ROI within 12-24 months, though this varies based on current inefficiencies and implementation scope. Quick-win components like slotting optimization or picking area redesigns often pay back within 3-6 months. For new facilities, design optimization typically adds 3-8% to construction costs while delivering 15-30% operational improvements, resulting in rapid payback.
Should I work with warehouse design specialists or use internal resources?
While internal teams understand your business intimately, warehouse design specialists bring specialized expertise and objective perspective that typically delivers superior results. The best approach often combines internal operational knowledge with external design expertise. For complex projects, engaging specialists usually delivers substantial ROI through better space utilization and operational efficiency that would be difficult to achieve with internal resources alone.
How do I balance current needs with future flexibility in warehouse design?
Prioritize modular, reconfigurable solutions over highly specialized fixed systems whenever possible. Utilize standardized dimensions and clear-span construction to preserve future options. Invest in appropriate infrastructure (power, data, floor specifications) that supports future technology adoption. Finally, incorporate scenario planning into your design process to evaluate how well proposed designs accommodate various potential future states.
How often should warehouse layout and design be reevaluated?
Most operations benefit from annual layout reviews, with minor optimizations implemented based on changing business requirements. More comprehensive redesigns typically occur on 3-5 year cycles or when significant business changes occur, such as new product lines, channel expansion, or volume growth. Regular slotting optimization (repositioning inventory based on activity patterns) should occur quarterly for most operations.
Recent blogs
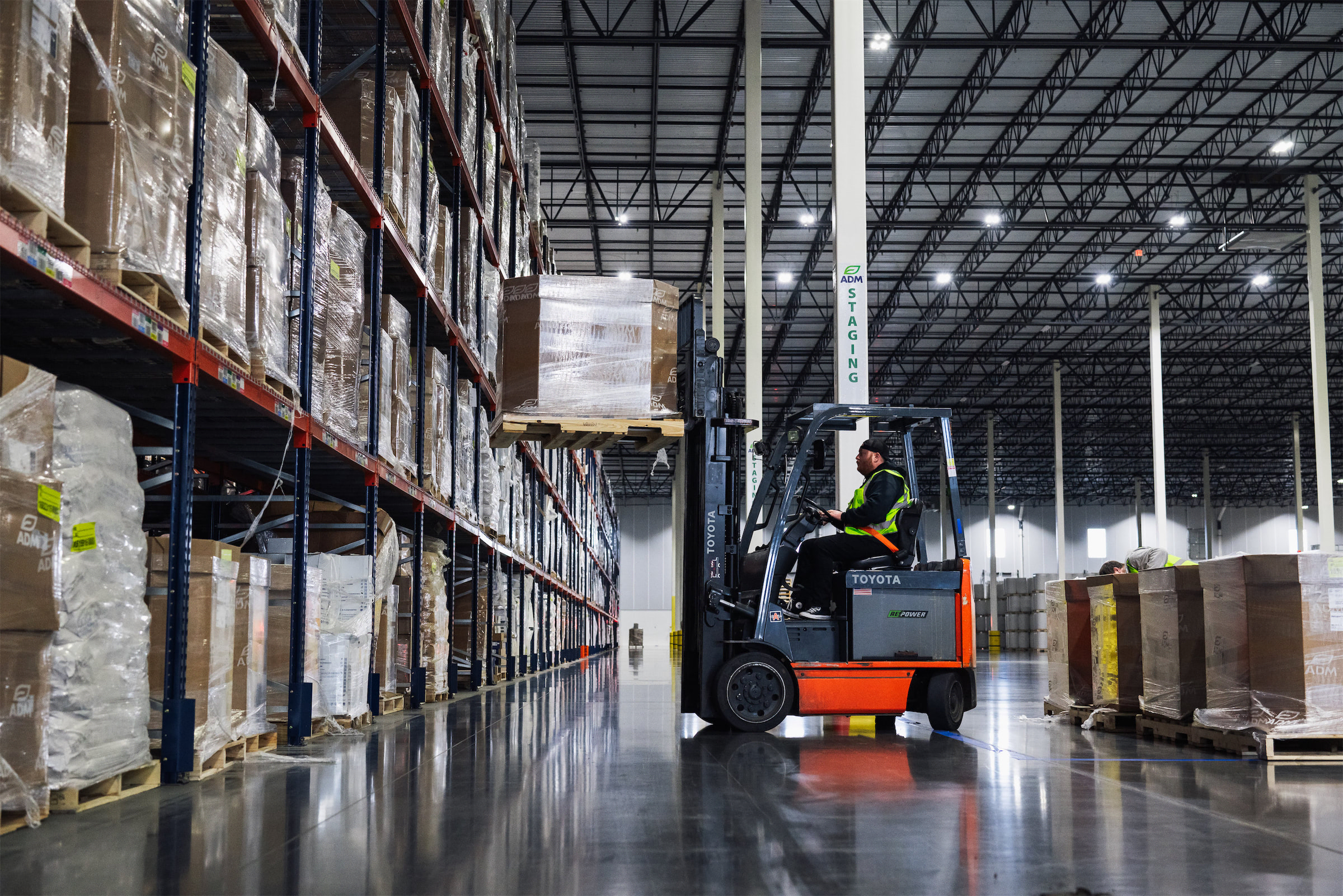
Peak Season Playbook: Scaling Warehouse Operations
Every operations manager knows the peak season paradox: you need double the warehouse capacity and triple the labor force for three months, but you can't afford to maintain those resources year-round. This guide reveals proven strategies for scaling efficiently during demand spikes while controlling costs.
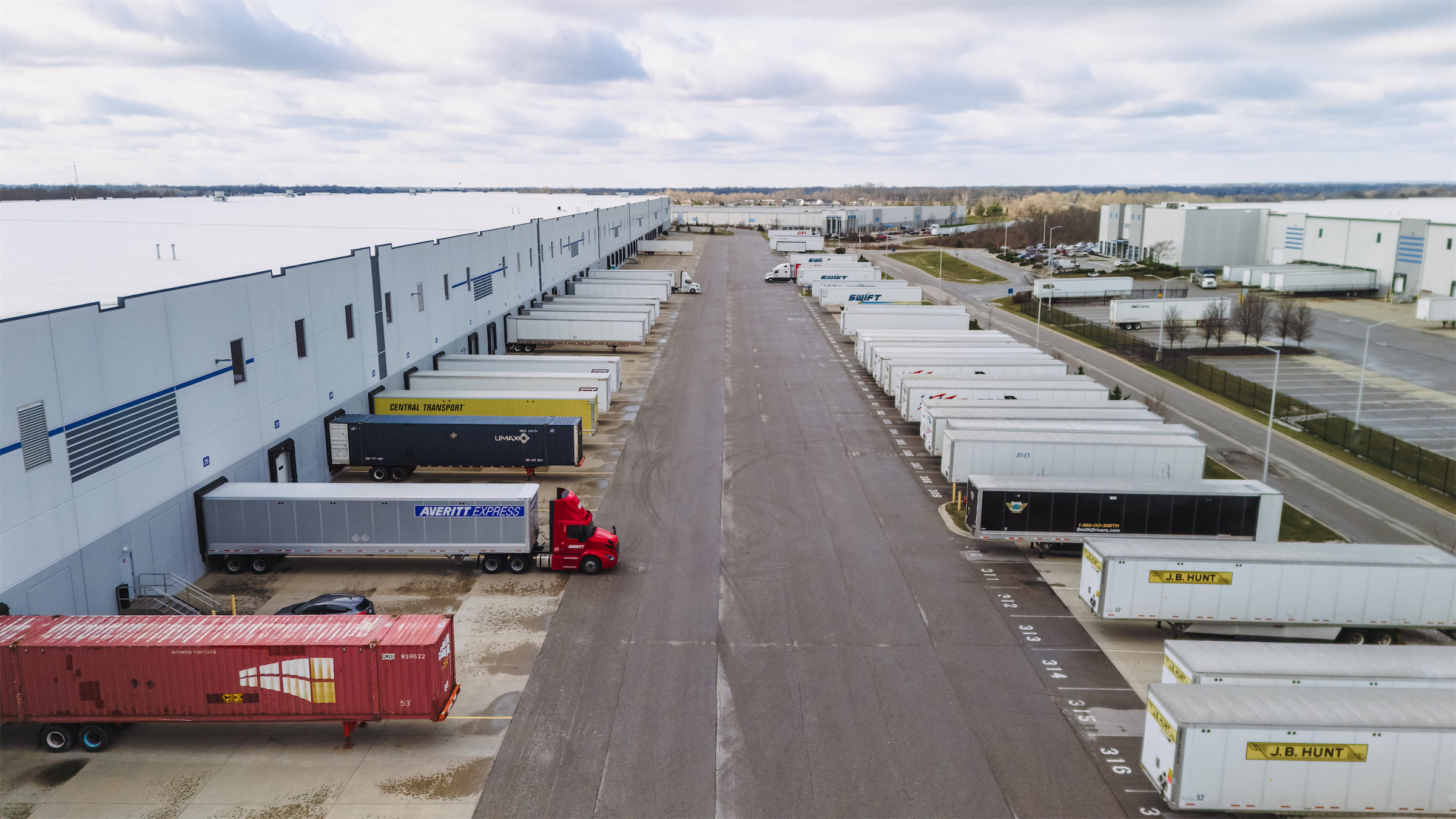
Build vs. Buy: The CFO's Guide to Warehousing Decisions
The warehousing decision facing your company seems straightforward: build your own facility or outsource to a third-party logistics provider. But the financial implications extend far beyond comparing lease rates to construction costs, impacting everything from balance sheet structure to operational flexibility.
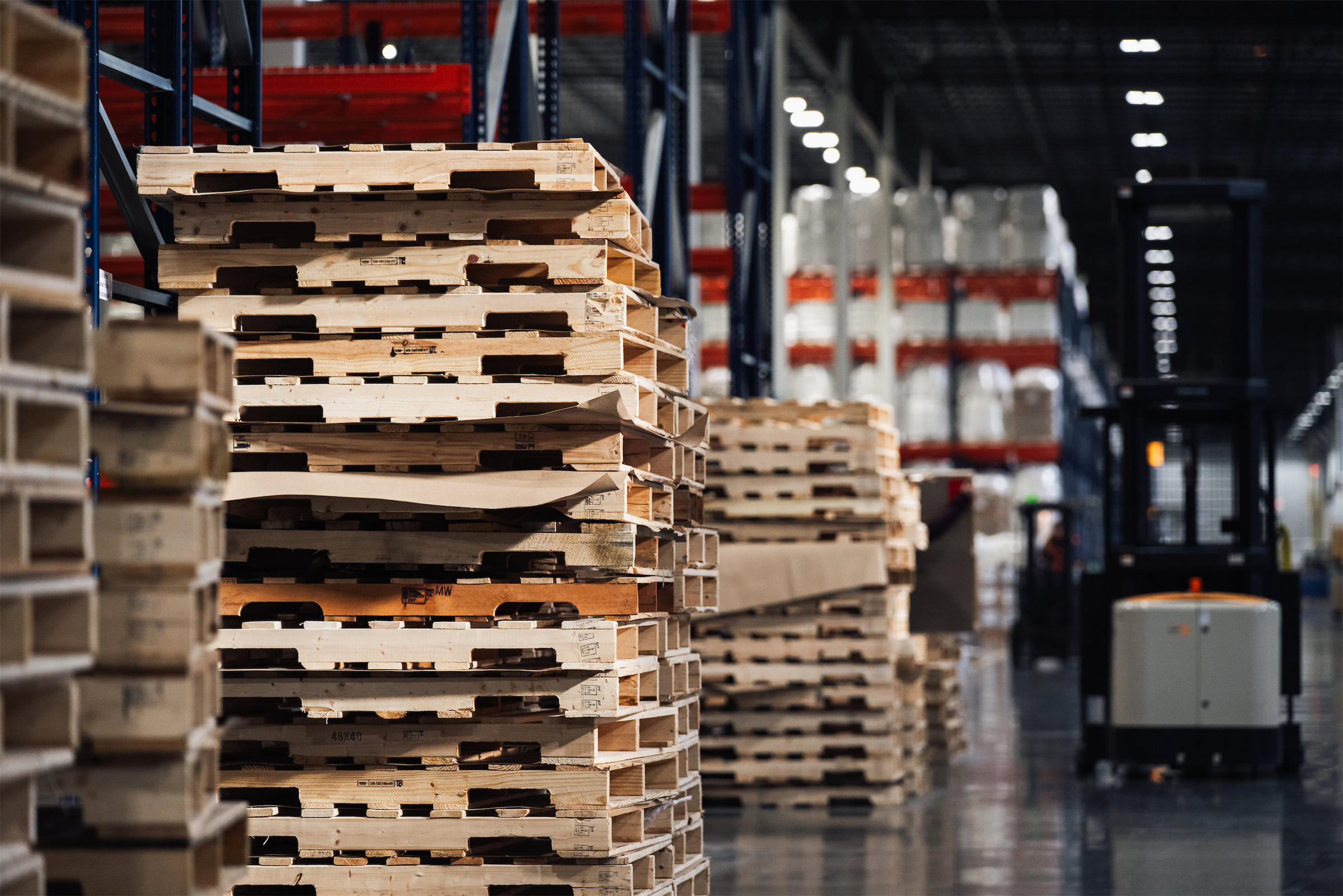
Omnichannel Fulfillment for CPG Brands: Unifying B2B and D2C from One Warehouse
Managing separate B2B and D2C fulfillment operations doubles complexity while fragmenting inventory visibility. Learn how unified omnichannel warehousing eliminates inefficiencies, prevents channel conflicts, and positions CPG brands for sustainable growth.
Arrange a visit
See the Commonwealth difference in action
We believe the best way to understand our capabilities is to experience them firsthand. We invite you to tour one of our facilities, meet our team, and discover how Commonwealth can optimize your logistics operations. Let us show you why so many businesses trust us with their supply chain needs.